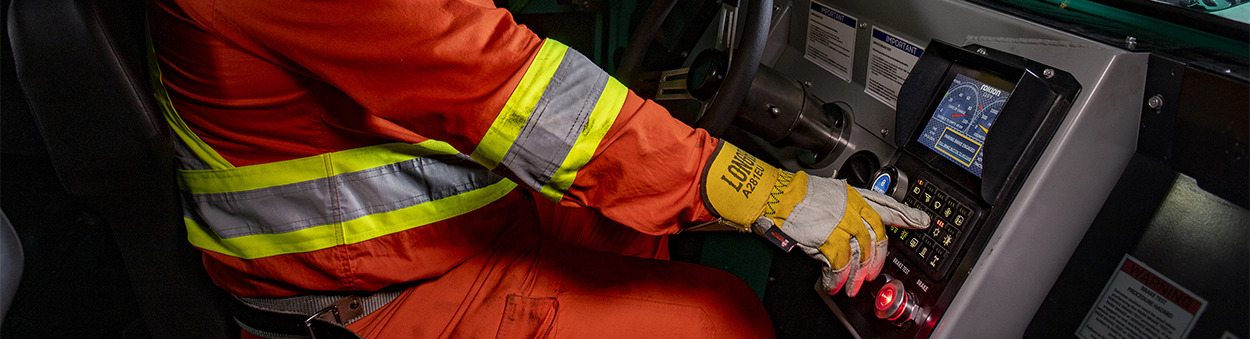
TECHNOLOGY
Rokion battery powered mining trucks are engineered with safety, efficiency, and ease of use in mind. Continuous engineering improvements mean that Rokion trucks can conform to the most sophisticated safety and performance requirements in mine sites around the globe.
VEHICLE SAFETY SYSTEMS
STANDARD ISSUE VEHICLE SAFETY SYSTEMS
Rokion battery electric mining vehicles incorporate multiple safety systems to ensure both the operator and passengers are kept safe in extreme mining environments. Each truck is designed to withstand the severity of rough terrain, high temperatures, abrasive conditions, and corrosive operating environments. During maintenance, electrical systems can be isolated and locked out from each truck's main power disconnect (high-voltage system) and control systems disconnect (low-voltage).
All Rokion trucks are equipped with multi-tiered control systems for safe operation during ramp descent and contain sophisticated controls for the battery, drive, and charging systems. Standard safety systems include:
- Traction Control
- Speed Limiters
- Safety Interlocks for the Charge and Drive Systems
- Seat Belts
- Fail-Safe Parking Brakes
- Safety Lighting (Strobes, Beacons, and Programmable LEDs)
- Backup Cameras
- and more...
OPTIONAL VEHICLE SAFETY SYSTEMS
Speed Zone Control System
Different operational areas within the mine often require different maximum travel speed limits. The optional Speed Zone Control system automatically reduces a Rokion truck's maximum travel speed upon entering certain areas of the mine. A mine site can define these low-speed areas based on hazardous ground conditions, high traffic volume, common personnel areas, or any other safety considerations they may have.
Driver Profile System
The optional Driver Profile system appoints different travel speed limits for different operators. A mine site can define speed limits based on ground conditions throughout the mine or based on operator responsibilities. For example, a site may designate an emergency response personnel profile which grants these operators a greater travel speed than a standard operator. During training, teaching staff can ensure that new drivers stay under a pre-determined travel speed to conform to any of the mine site's safety policies.
Ramp Control Systems
Rokion's Regenerative Braking, Integrated Brake Resistor, and Adaptive Speed Control systems work in conjunction with a ramp truck's standard service brakes and fail-safe brakes to ensure safe operation during ramp descent.
Learn More About Rokion's Ramp Control Systems
BATTERY POWER & CHARGING
Lithium Iron Phosphate (LiFePO4) Battery Technology
All Rokion trucks are equipped with lithium iron phosphate (LiFePO4) battery technology. This technology is the safest reusable battery technology available and SHOULD NOT be confused with lithium polymer, lithium cobalt or lithium magnesium battery technologies that can be unstable and hazardous to operate if not managed properly.
Unlike lead acid batteries, LiFePO4 batteries do not discharge gas during charge cycles, eliminating the need for unique ventilation systems. LiFePO4 batteries are safe, require no maintenance, and are a reliable energy storage device.
The Battery Module itself is made up of sealed battery cells that can be arranged to fit a variety of power requirements. These battery cells are not user serviceable and are sealed inside the battery module, offering an additional level of operator and passenger safety.
The Battery Module is internally fused so that, in the unlikely event of a short circuit, the fuse will open and safely isolate the power within that module. In this instance, the failed battery module would be swapped out for a spare module and then sent back to Rokion for repair. Replacing a Battery Module this way allows for the highest amount of safety for both operators and maintenance personnel and requires no special training or tools to replace a Battery Module.
Battery Management System (BMS)
All Rokion trucks contain a sophisticated Battery Management System (or BMS) which is responsible for monitoring and controlling all power systems to ensure the utmost level of operator safety is achieved. The BMS constantly monitors the battery system to protect it from excess charge or discharge current, or from voltage that might be unintentionally applied.
The BMS is responsible for monitoring the Battery Module voltages, currents, temperatures, state of charge, and states of health of each individual cell and of the Battery Module as a whole. If safety limits are exceeded, the BMS will shut down either the electrical load or the battery charger, whichever is causing the condition. Temperature is monitored and the vehicle discharge or charge state is controlled by the BMS as an additional safety feature. The BMS also calculates the current level of charge, which is displayed on the User Interface Module along with indicators from the BMS for low battery pack and full battery pack conditions.
Battery Charger
Rokion trucks are equipped with SAE J1772 Charge Connectors. The SAE J1772 charging system is a North American standard used to charge the vast majority of electric vehicles in North America. This ensures that no special adapters or proprietary components are required when introducing a Rokion vehicle into an operation.
There are multiple levels of safety redundancy in place when charging a Rokion truck:
- The charger itself is not a typical lead acid battery charger; it is designed to be intelligent and to detect any problems with the battery pack, shutting itself down if necessary.
- The BMS monitors each cell as well as the pack as a whole and is capable of disconnecting the charger via a relay.
- A relay within the charger requires power in order to operate. In the event that control power is lost, the charger is disabled.
Rokion has made every effort to ensure the battery charging system is as safe and as user-friendly as possible.
RAMP CONTROL SYSTEMS
RAMP DESCENT
Rokion's regenerative braking system, Integrated Brake Resistor and Adaptive Speed Control software work together along with the vehicle's standard service and fail-safe brakes to ensure safe operation during ramp descent.
Regenerative Braking
Rokion’s regenerative braking system uses the electric motor from each Drive Module as both a motor brake and as an energy generator. Regenerative braking allows the electric motors to slow the vehicle down while simultaneously adding charge to its Battery Modules and preserving its mechanical brakes.
Regenerative braking is manually activated by releasing the accelerator pedal while in forward motion and is automatically activated as it reaches it’s pre-programmed speed limit while on ramp descent. This ensures the vehicle maintains a steady and predictable rate of travel as it safely descends ramps of up to 20% grade, while safeguarding brake and drive components from excessive wear.
Integrated Brake Resistor
On ramp descent, the regenerative braking system generates energy that is stored in the vehicle’s Battery Modules. To ensure there is sufficient storage space for this incoming regenerative energy, the Integrated Brake Resistor draws energy from the Battery Modules as they approach 92% capacity. This energy is converted to heat which is then redirected to the truck's cooling or ventilation systems.
Adaptive Speed Control
The purpose of Adaptive Speed Control is to regulate vehicle speed, acting as a fail-safe control for the regenerative braking system.
By adjusting vehicle speed, the Integrated Brake Resistor is never overwhelmed as it diverts energy from the vehicle’s battery modules in advance of incoming regenerative energy. This control process maintains a state of balance between the outgoing energy consumed by the Integrated Brake Resistor, and the incoming energy produced by the regenerative braking system.
Adaptive Speed Control protects the Battery Modules by slowing the vehicle down when the batteries are unable to store incoming regenerative power at a high rate. By preserving the Drive Modules from the mechanical stress associated with ramp travel, Adaptive Speed Control facilitates safe and reliable ramp descent.
RAMP ASCENT
Intelligent Power Delivery
Rokion's objective was to engineer a truck that could perform far beyond the grade, distance, and depth found in typical ramp access mine. On ramp ascent, Rokion trucks can navigate a 20% grade at full GVWR, driving at its maximum programmed speed over a distance of 13 km*, for a total vertical rise of 2500 m. With enough power to climb a 100% grade (45 degree) ramp, Rokion utility and crew trucks are equipped to safely and efficiently handle the steepest ramps.
*Approximated — this distance would be sufficient for all but the longest ramps in the world.
Drawbar Force
Rokion battery powered trucks use electric motors and gearboxes designed for lower speeds and higher torque, attributes which are ideal for mine application and ramp use. Conventional all-wheel drive trucks, including those designed for pulling, compromise on torque and drawbar force to preserve speed and acceleration for legal road use.
Rokion trucks not only have a higher drawbar force, but their power control systems provide intelligent power delivery and traction control for unmatched ramp navigation.
MODULAR PLATFORM ARCHITECTURE
Rokion battery powered trucks are engineered with a patented modular system designed for ease of serviceability. Modular vehicle components are simply interchanged when service is required. While one Battery or Drive Module is being serviced, the other module is in operation. This modular system minimizes downtime, ensures vehicle availability, and increases mine asset productivity.